In the world of metal finishing, anodizing and hard anodizing are pivotal processes, particularly in CNC machining. These techniques not only enhance the aesthetic appeal of metal components but also significantly improve their durability and resistance to wear and corrosion.
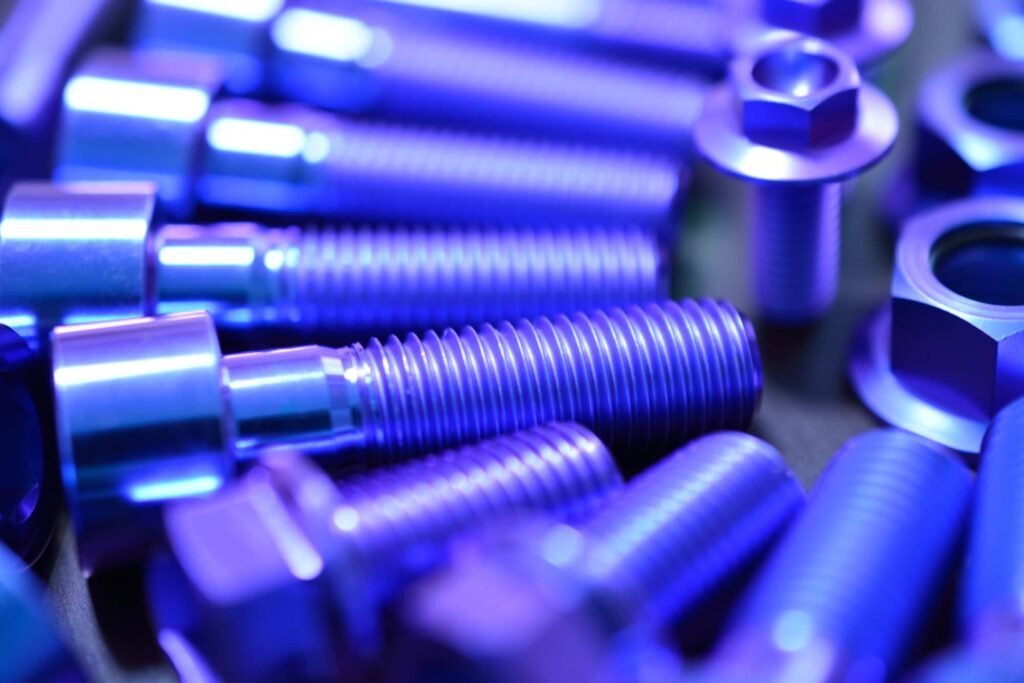
Understanding Anodizing and Hard Anodizing
Anodizing: What is it?
The electrochemical process of anodizing creates a protective oxide layer on metal surfaces, mostly aluminum. This layer offers a foundation for coloring and improves resistance to wear and corrosion. By submerging the metal in an electrolytic solution and running an electric current through it, a thin yet resilient oxide coating is created.
Hard Anodizing: What Is It?
A more sophisticated type of anodizing that produces a thicker and harder oxide layer is called hard anodizing, sometimes referred to as Type III anodizing. Higher current densities and lower temperatures are used in this technique to provide a coating with better hardness and wear resistance. Components used in the automotive and aerospace industries that demand extraordinary endurance are best suited for hard anodizing.
The Procedure for Anodizing
Cleaning: To get rid of any impurities that can interfere with the anodizing process, the metal component is meticulously cleaned.
Etching: By preparing the surface, a chemical etch improves the oxide layer’s adherence.
Anodizing is the process of producing the oxide layer by immersing the part in an electrolyte solution, usually sulfuric acid, and applying an electric current.
Sealing: To increase corrosion resistance and color stability, the anodized portion is sealed to plug the oxide layer’s pores.
Important Features of Hard Anodizing
- Thickness: A strong surface layer is produced by hard anodized coatings, which normally have a thickness of 25 to 100 microns.
- Hardness: On the Rockwell C scale, the coating can reach a hardness of 65 to 70, which is equivalent to hardened tool steel.
- Resistance to Wear and Corrosion: Provides noticeably better resistance to wear and corrosion than conventionally anodized or untreated aluminum.
- Excellent electrical insulating qualities are provided by the oxide layer.
Design Factors for CNC-Made Components
Selection of Materials
Hard anodizing is not appropriate for every aluminum alloy. The following are suggested:
- 6061: is a general-purpose alloy that works well for harsh anodizing.
- 7075: Known for its great strength, this material creates an extremely hard anodized surface.
- 5052: Provides excellent resistance to corrosion, making it appropriate for maritime settings.
Dimensional Factors
- Coating Growth: Part dimensions are impacted by the coating’s 50% inward growth and 50% outward growth.
- Minimum Inside Radii: Design with minimum inside radii of 0.015″ to 0.030″ to prevent coating buildup and cracking.
- Threads and Holes: External threads should be undersized, and holes may need reaming post-anodizing for precision fits.
Surface Finish
- Pre-Anodize Finish: A smoother initial surface will result in a smoother anodized finish.
- Color Options: Although dyes can be employed to provide a variety of colors, uniformity can be difficult, hard anodizing naturally yields a gray to charcoal color.
Hard Anodizing Applications in CNC Machining
Aircraft
Structural Elements: The strength-to-weight ratio of hard anodized aluminum is exceptional.
Wear-resistant parts are advantageous for parts such as control surfaces and actuators.
Automobile
- Engine Parts: Increased wear resistance is advantageous for cylinder liners and pistons.
- Aesthetic Trim: Gives external and interior components a long-lasting polish.
Electronics for consumers
- Device Housings: Gives casings a high-end feel and scratch resistance.
- Heat Sinks: Make effective use of the thermal characteristics to dissipate heat.
Industrial Equipment
- Hydraulic Components: Improved valve and piston wear resistance.
- Cutting Tools: Greater surface hardness results in longer tool life.
Obstacles and Restrictions
- Fatigue Strength: The basic material’s fatigue strength may be marginally diminished by hard anodizing.
- Coating Thickness Variability: It might be difficult to maintain uniform thickness throughout intricate geometries.
- Cost: Typically, this is more costly than traditional anodizing.
- Color Restrictions: Compared to traditional anodizing, it is more challenging to get consistent, vivid colors.
In conclusion
A strong surface treatment that greatly improves the functionality and durability of CNC-machined aluminum components is hard anodizing. You may use hard anodizing to produce high-quality components for a range of applications if you comprehend the procedure, its advantages, and design considerations. For the greatest anodizing outcomes, keep in mind to select the right aluminum alloys, take dimensional changes into consideration, and streamline your CNC machining procedure. Working together with your anodizing and manufacturing partners will guarantee the optimum results for your particular applications.
For additional information and expert anodizing services, think about getting in touch with professionals in the field who can offer solutions that are customized to your unique requirements. Investigate the possibilities of hard anodizing for your upcoming CNC machining project and enjoy the advantages of improved performance and durability.
Key Automotive Components That Rely on CNC Machining
Everything You Need To Know About Anodizing
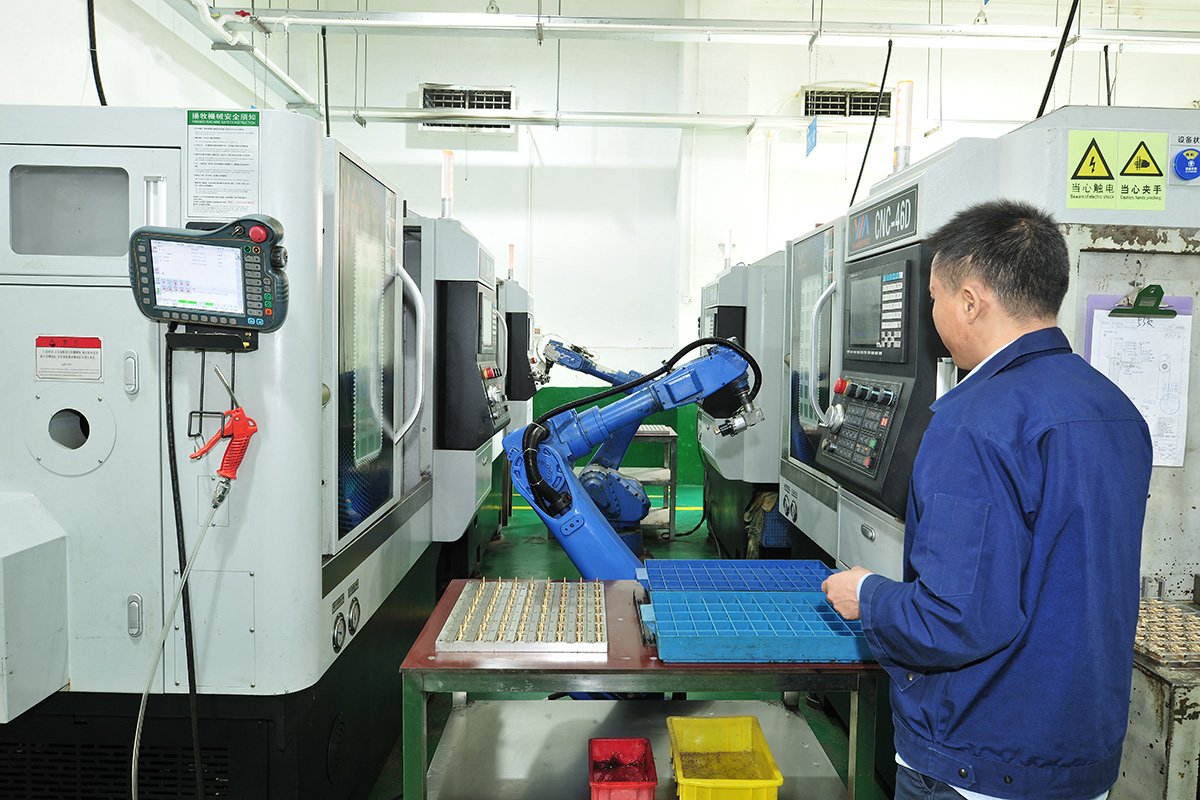