CNC (computer numerical control) machining has emerged as a key technology in the fast-paced world of contemporary manufacturing, producing intricate and accurate parts with unmatched efficiency. The number of axes a machine has determines its capabilities, versatility, and the complexity of the geometries it can machine in every facet of CNC machining. We will examine 3-axis, 4-axis, and 5-axis CNC machines in detail in this post, highlighting their internal mechanisms, uses, and main distinctions.
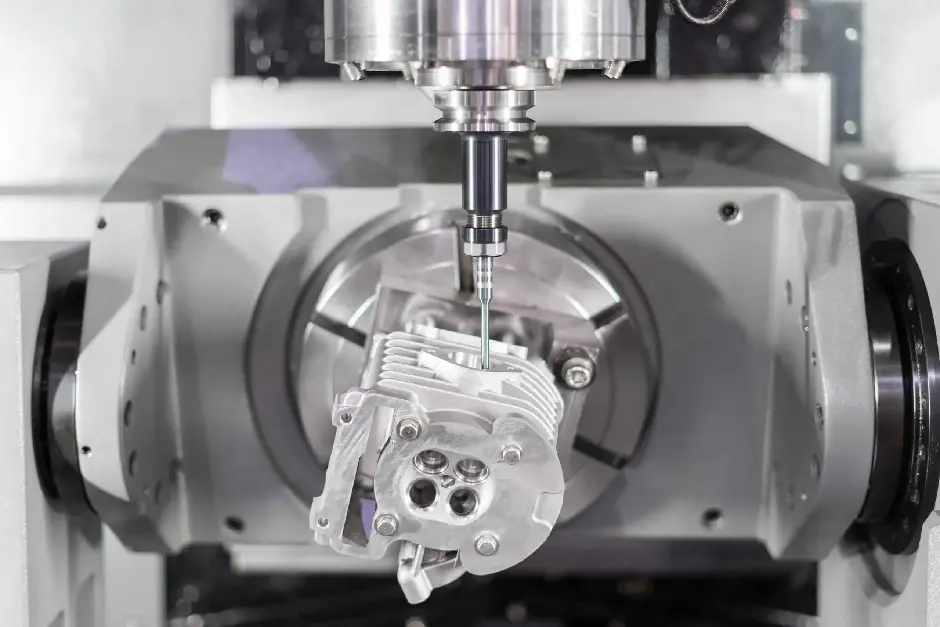
Discover the Fundamentals of CNC Machining Axes
Understanding the meaning of 3, 4, and 5-axis CNC machines is crucial before comparing them. An axis is the direction a machine can move in CNC machining. The X-axis, which extends horizontally from left to right, the Y-axis, which moves vertically up and down, and the Z-axis. Which extends horizontally toward and away from the machine operator, are the three primary axes. All CNC machines, regardless of the number of axes, have these three axes, which serve as the foundation for the three-dimensional space in CNC machining. CNC machines can have rotary axes in addition to the linear X, Y, and Z axes. Because they rotate around the X, Y, and Z axes, these rotary axes are known as the A, B, and C axes, respectively. The machine tool’s range of motion is greatly increased, and more intricate geometries can be created with the addition of rotary axes.
3-Axis CNC Machining
The Foundation of Precision
3-axis CNC machining is the most fundamental and widely used form of CNC machining. As the name implies, a 3-axis CNC machine operates along the X, Y, and Z axes, allowing for precise movement in three-dimensional space. In a typical 3-axis machining setup, the workpiece is securely clamped in place on the machine table. The cutting tool, held by the spindle, moves along the X, Y, and Z axes to remove material from the workpiece and create the desired shape.
Capabilities and Applications
3-axis CNC machines are well-suited for a wide range of applications, particularly those that involve the production of relatively simple 2D and 2.5D geometries. They excel at tasks such as milling flat surfaces, cutting slots, drilling holes, and creating basic contours. Due to their simplicity and versatility, 3-axis CNC machines are commonly used in industries such as automotive, aerospace, electronics, and general manufacturing to produce components such as brackets, plates, gears, and housings.
Limitations
While 3-axis CNC machines are highly capable, they do have certain limitations. One of the primary limitations is their inability to machine complex 3D geometries that require multi-sided or multi-angled machining. Since the workpiece remains stationary in a fixed position, accessing all sides of the workpiece often requires repositioning or additional fixtures. Which can be time-consuming and may introduce errors. Additionally, 3-axis machines may struggle to produce parts with intricate internal features or undercuts. The cutting tool’s movement is restricted to the three linear axes.
4-Axis CNC Machining
Expanding the Horizons of Precision
4-axis CNC machining builds upon the capabilities of 3-axis machining by adding a rotational axis, typically the A-axis. The A-axis allows the workpiece to rotate around the X-axis, providing the machine with an extra degree of freedom and enabling the creation of more complex geometries. In a 4-axis machining setup, the spindle still moves along the X, Y, and Z axes, while the workpiece rotates on the A-axis. Allowing the cutting tool to access different sides of the workpiece without the need for repositioning.
Capabilities and Applications
The addition of the A-axis significantly expands the range of applications for 4-axis CNC machines. They are particularly well-suited for tasks that require machining parts with angled features, such as tapered holes, helical grooves, and camshafts. 4-axis machines are also commonly used in the production of parts that require multi-sided machining, as they can access all four sides of the workpiece in a single setup. This reduces the need for additional fixtures and minimizes the risk of errors associated with repositioning the workpiece.
Types of 4-Axis Machining
There are two main types of 4-axis machining: continuous and indexing. In continuous 4-axis machining, the workpiece rotates continuously on the A-axis while the cutting tool removes material, allowing for the creation of complex profiles and surfaces. Indexing 4-axis machining, on the other hand, involves rotating the workpiece to a specific angle on the A-axis and then performing a machining operation. The workpiece is then rotated to the next angle, and the process is repeated until the desired shape is achieved.
5-Axis CNC Machining
Unleashing the Full Potential of Precision
5-axis CNC machining represents the pinnacle of CNC machining technology, offering the highest level of precision, versatility, and complexity. A 5-axis CNC machine combines the capabilities of 3-axis and 4-axis machines with an additional rotational axis, typically the B-axis or C-axis. The B-axis allows the workpiece to rotate around the Y-axis, while the C-axis enables rotation around the Z-axis. The combination of these two additional rotational axes provides the machine with five degrees of freedom, allowing it to access any point on the workpiece from virtually any angle.
Capabilities and Applications
5-axis CNC machines are capable of producing the most complex 3D geometries with exceptional precision and surface finish. They are widely used in industries such as aerospace, medical, mold and die, and high-end automotive. Where the production of intricate and high-precision parts is essential. 5-axis machines excel at tasks such as machining turbine blades, impellers, prosthetics, and complex molds. Where traditional 3-axis and 4-axis machines may struggle to achieve the required level of accuracy and complexity.
Types of 5-Axis Machining
There are two main types of 5-axis machining: fully continuous 5-axis machining and 3 + 2 machining. In fully continuous 5-axis machining, all five axes of the machine move simultaneously. Allowing for the creation of highly complex 3D shapes with smooth and continuous surfaces. 3 + 2 machining, on the other hand, involves using the three linear axes (X, Y, and Z) in combination with two rotational axes (A and B or A and C) to perform machining operations. In 3 + 2 machining, the rotational axes are used to position the workpiece at a specific angle, and then the machining operation is performed using the linear axes.
Comparing 3-Axis, 4-Axis, and 5-Axis CNC Machines
Now that we have a comprehensive understanding of 3-axis, 4-axis, and 5-axis CNC machines, let’s compare their key characteristics, capabilities, and limitations.
Axis Configuration and Movement
- 3-Axis: Operates along the X, Y, and Z linear axes, with the workpiece remaining stationary.
- 4-Axis: Adds a rotational axis (A-axis) to the 3-axis configuration, allowing the workpiece to rotate around the X-axis.
- 5-Axis: Incorporates two additional rotational axes (A and B or A and C) to the 3-axis configuration, providing the machine with five degrees of freedom.
Geometric Complexity
- 3-Axis: Best suited for simple 2D and 2.5D geometries, with limited ability to machine complex 3D shapes.
- 4-Axis: Can produce more complex geometries with angled features and multi-sided machining capabilities.
- 5-Axis: Capable of machining the most complex 3D geometries with exceptional precision and surface finish.
Fixturing and Setup
- 3-Axis: Often requires additional fixtures and repositioning to machine multiple sides of the workpiece.
- 4-Axis: Reduces the need for additional fixtures and repositioning, as the workpiece can be rotated to access different sides.
- 5-Axis: Minimizes the need for fixtures and repositioning, as the machine can access any point on the workpiece from virtually any angle.
Machining Efficiency
- 3-Axis: Generally slower for complex parts, as multiple setups and repositioning may be required.
- 4-Axis: Offers increased machining efficiency for parts with angled features and multi-sided machining requirements.
- 5-Axis: Provides the highest machining efficiency for complex 3D parts, as it can complete the machining process in a single setup.
Cost
- 3-Axis: The most cost-effective option, as it has a simpler design and fewer components.
- 4-Axis: Slightly more expensive than 3-axis machines, due to the addition of the rotational axis.
- 5-Axis: The most expensive option, as it requires more advanced technology and components to support the additional rotational axes.
Choosing the Right CNC Machine for Your Needs
Selecting the appropriate CNC machine for your manufacturing needs is a critical decision that can significantly impact the quality, efficiency, and cost of your production process. When choosing between 3-axis, 4-axis, and 5-axis CNC machines, consider the following factors:
Part Complexity
- If your parts are relatively simple, with mostly 2D or 2.5D geometries, a 3-axis CNC machine may be sufficient.
- For parts with angled features, multi-sided machining requirements, or moderate complexity, a 4-axis CNC machine may be a better choice.
- If your parts are highly complex, with intricate 3D geometries and tight tolerances, a 5-axis CNC machine is likely the best option.
Production Volume
- For low-volume production runs, a 3-axis CNC machine may be the most cost-effective choice, as it has a lower initial investment and operating costs.
- As production volume increases, the efficiency advantages of 4-axis and 5-axis machines may offset their higher initial costs, making them more cost-effective in the long run.
Budget
- Consider your budget constraints when choosing a CNC machine. 3-axis machines are generally the most affordable, while 4-axis and 5-axis machines can be significantly more expensive.
- However, it’s important to balance cost with the capabilities and performance required for your specific applications. Investing in a higher-axis machine may be worth it if it allows you to produce parts more efficiently and with higher quality.
Operator Skill Level
- 3-axis CNC machines are generally easier to operate and program, making them a good choice for beginners or operators with limited experience.
- 4-axis and 5-axis machines require more advanced programming and operating skills, as they involve additional rotational axes and more complex machining operations.
- Consider the skill level of your operators when choosing a CNC machine, and provide appropriate training and support if necessary.
Conclusion
In conclusion, 3-axis, 4-axis, and 5-axis CNC machines each offer unique capabilities and advantages, making them suitable for different types of manufacturing applications. 3-axis machines form the foundation of precision machining and are well-suited for simple 2D and 2.5D geometries. 4-axis machines expand the horizons of precision by adding a rotational axis, enabling the production of more complex parts with angled features and multi-sided machining capabilities. The most advanced CNC machining technology is represented by 5-axis machines. Which provides the highest degree of complexity, precision, and adaptability for creating the most complex 3D geometries.
When choosing a CNC machine for your manufacturing needs, it’s essential to carefully consider the factors discussed above, including part complexity, production volume, budget, and operator skill level. By selecting the right CNC machine for your specific applications, you can optimize your production process, improve the quality of your parts, and enhance your competitiveness in the global manufacturing marketplace.
Exploring the World of Industrial CNC Machining
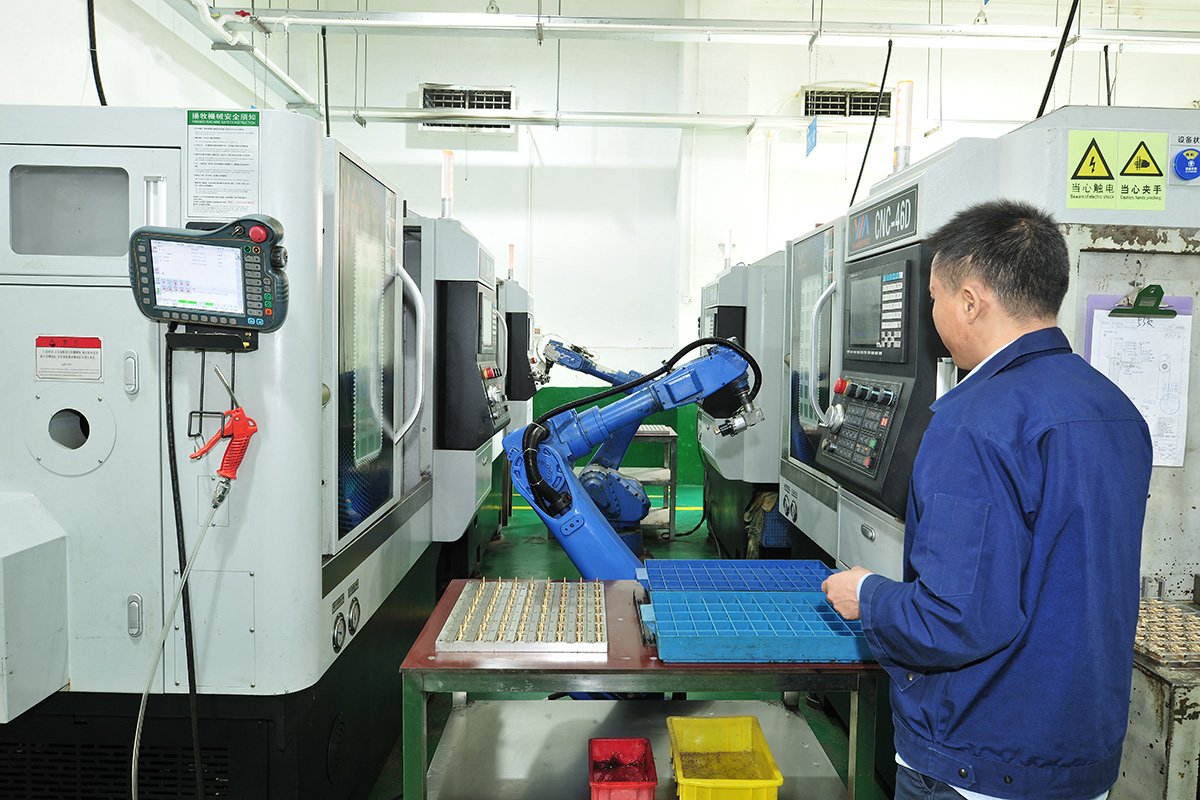