CNC (computer numerical control) processing technology is a shining protagonist in modern manufacturing. With the magical power of digital control, it accurately transforms design blueprints into precision parts and is widely used in many core fields such as automobiles, aerospace, electronics, and molds. CNC processing is like a precise symphony, in which each processing method is a unique note, combining an efficient and precise manufacturing movement.
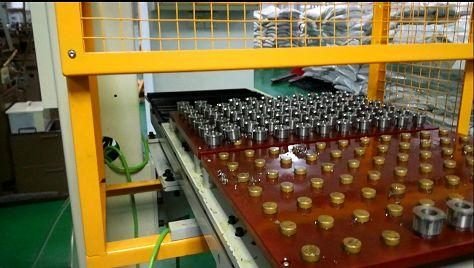
Turning: Precision carving during rotation
Turning is one of the most basic and common processing methods in the field of CNC processing. It is like a skilled engraver who carves the workpiece precisely during rotation. Its working principle is l ike a carefully choreographed dance. The workpiece rotates happily, and the tool steadily cuts the surface of the workpiece, finally perfectly presenting the required shape and size. Turning is particularly good at processing circular parts. Whether it is slender shaft parts, flat disc parts, or hollow sleeve parts, they can be easily formed under its “magic hands”.
The advantages of turning are very significant. Its processing speed is like lightning. When mass-producing circular workpieces, it shows unparalleled efficiency advantages, which makes other processing methods far behind. CNC lathes are like an all-around player. They can easily complete various cutting operations such as outer circles, inner circles, and end faces to ensure that the processing accuracy reaches a very high level. During the turning process, the tool is like a nimble dancer. Through clever adjustments at different angles, it can also elegantly complete complex processing actions such as chamfering and thread cutting. In the manufacture of automobile engines, turning plays an irreplaceable and important role in the processing of key parts such as crankshafts and camshafts.
Application
In applications, turning can be seen everywhere. Take the crankshaft of an automobile engine as an example. It is a key component of the engine with a complex shape and extremely high precision requirements. Through turning, key parts such as the main journal and connecting rod journal of the crankshaft can be accurately shaped to ensure that their dimensional accuracy and surface roughness meet the design standards. Thereby ensuring stable and efficient operation of the engine. In the field of medical devices, some precision surgical instruments, such as intramedullary nails in orthopedic surgery, also rely on turning. Intramedullary nails require precise outer diameter dimensions, smooth surfaces, and specific thread structures. Turning, with its high precision and flexibility, can meet these strict requirements and provide reliable guarantees for the smooth progress of the operation. In addition, turning is used to produce various small and precise shaft parts in the manufacture of high-end watch movements. These parts’ machining accuracy directly affects the watch’s travel time accuracy. Turning ensures that each part can meet the micron-level precision standard.
Milling: Multi-blade Rotation Artistic Creation
Milling is like a multi-blade rotation art feast. Through the high-speed rotation of multi-blade tools, the workpiece is cut and processed, and various complex geometric shapes, such as planes, grooves, holes, etc,. can be easily created. CNC milling machines are like a creative artist with strong processing flexibility. They can freely change the tool path according to design requirements and easily overcome the processing problems of complex contours.
The charm of milling lies in its ability to handle more complex workpiece shapes. Whether it is a three-dimensional shape, an inclined slope, or a smooth curved surface, it can handle it with ease. Milling can be divided into plane milling, forming milling, milling holes, and other types, each of which has its unique application scenarios. In modern manufacturing, CNC milling machines also support multi-axis processing. This powerful function greatly improves the accuracy and complexity of processing, making it an indispensable force in the automotive, aviation, mold, machinery, and other industries. In the processing of aircraft engine blades, milling can accurately shape the complex curved surface of the blade to ensure the efficient operation of the engine.
Drilling: An efficient expert in precise drilling
Drilling plays an important role in CNC machining. It is a common method for machining cylindrical holes in workpieces. It is like an accurate shooter, able to quickly and accurately punch the required holes on the workpiece. Modern CNC equipment has given drilling more possibilities. It can not only perform conventional simple drilling, but also complete deep hole processing. Hole expansion, tapping, and other complex operations are required to meet the strict requirements of different processes.
The biggest advantage of drilling is its high efficiency, which can obtain an accurate hole shape and hole diameter in a short time. In many fields, such as mechanical processing and electronic and electrical equipment production, drilling technology is an indispensable key link. In the manufacturing process of circuit boards, a large number of precise holes need to be drilled on tiny circuit boards. CNC drilling equipment can complete this task quickly and accurately to ensure the accurate installation of electronic components.
Grinding: A Finely Polished Surface Artist
Grinding is like a surface artist pursuing perfection. It mainly uses the cutting action of abrasives to finely polish the workpiece to improve the surface finish and dimensional accuracy of the workpiece. It can not only remove a small amount of excess material on the surface of the workpiece, but also, like a magician, elevate the surface quality of the part to a whole new level. CNC grinders are widely used in the field of processing parts with high hardness materials and strict requirements for high precision and surface finish.
Grinding includes surface grinding, external cylindrical grinding, internal cylindrical grinding, and other methods. Each method can achieve very high dimensional accuracy, so it is usually used in the finishing stage. For some special materials or parts with complex shapes, grinding is an effective processing method. In the manufacture of precision bearings, grinding can make the bearing surface achieve an extremely high finish and precision, ensuring the smooth operation and service life of the bearing.
Electrospark machining
Electrical discharge machining (EDM) is a very distinctive processing method in CNC machining, just like a magical discharge carving show. It uses the electric sparks generated between the electrode and the workpiece, like a tiny carving knife, to accurately remove a small amount of material from the surface of the workpiece. Thereby, carefully shaping the desired shape. Electrospark machining is very useful in the field of precision parts processing of hard materials and complex shapes. Especially in industries such as mold manufacturing, aerospace, and electronics, which have extremely high requirements for precision and complex shapes. It has a wide range of applications.
The unique advantage of electrospark machining is that it is completely independent of the hardness of the material. It can break through the limitations of traditional machining and can accurately machine complex details. Although its processing speed is relatively slow, it has always occupied an important position in some special fields due to its high precision and excellent processing capabilities for complex shapes. When manufacturing complex cavities for precision molds, electrospark machining can achieve precision and detail requirements that are difficult to achieve with traditional machining methods.
Laser cutting and water jet cutting: Pioneers of efficient and precise cutting
Laser cutting and water jet cutting are the pioneers of efficient and precise cutting in CNC machining. Laser cutting uses a high-energy laser beam, like focused sunlight, to locally heat the workpiece, causing the material to melt or vaporize instantly, thereby achieving precision cutting. Water jet cutting uses the powerful impact of high-pressure water flow and abrasives to cut the surface of the workpiece, like an invisible blade.
The significant advantages of these two cutting methods are that they do not produce mechanical stress and can process extremely complex and fine contours. And are suitable for a variety of materials, including metals, plastics, ceramics, etc. Laser cutting and water jet cutting are particularly suitable for processing thin plates, precision parts, and workpieces with complex shapes. In the processing of electronic product shells, laser cutting can achieve high-precision cutting to ensure the beauty and performance of the shell. Water jet cutting shows unique advantages in the processing of brittle materials such as stone and glass.
Conclusion
CNC processing technology, with the perfect collaboration of multiple processing methods such as turning, milling, drilling, grinding, EDM, laser cutting, and water jet cutting, is like a precision symphony orchestra, meeting the diverse needs of parts processing in various industrial production. From efficient turning and milling, to precision grinding and EDM, to laser cutting and water jet cutting in special cutting fields. Each processing method plays an irreplaceable and important role in its field, and together promote modern manufacturing to continuously move towards higher precision and efficiency peaks.
Key Automotive Components That Rely on CNC Machining
Everything You Need To Know About Anodizing
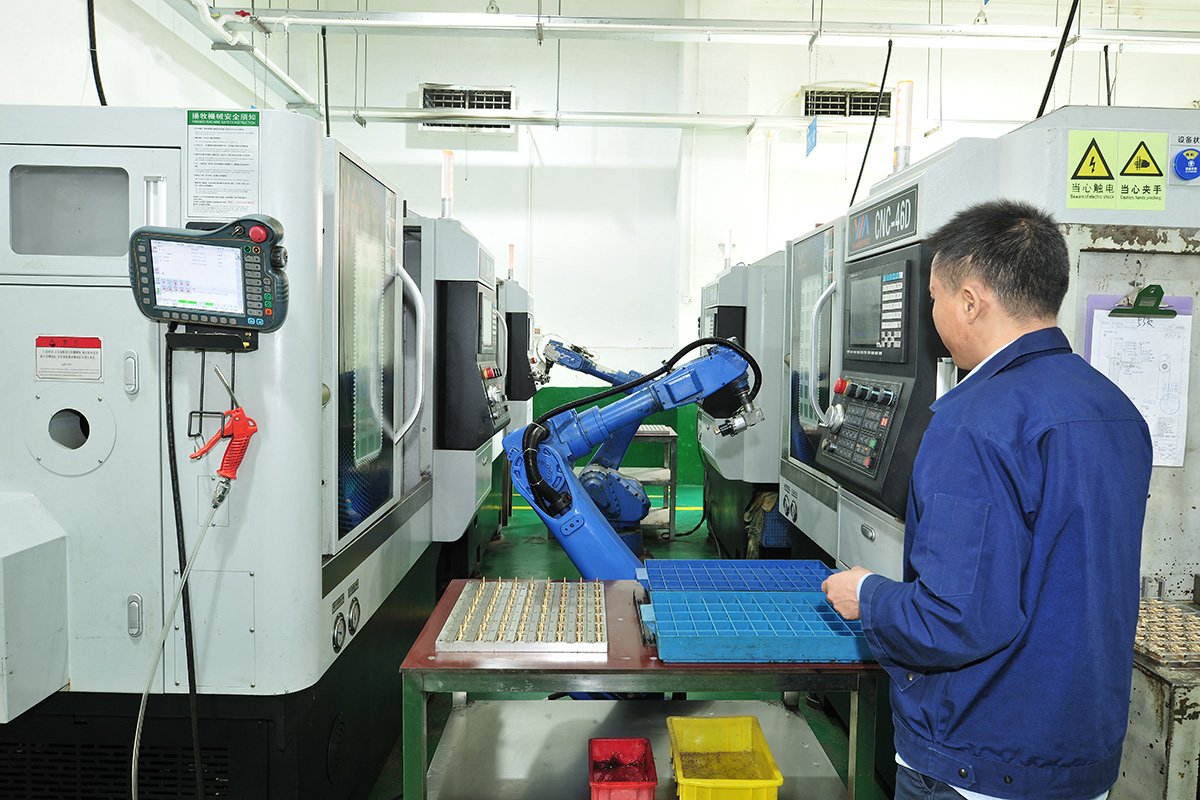